Like you, our Gun Techs™ Product Experts live the 2A lifestyle.
Our team of expert Gun Techs™ stands ready to offer unparalleled firearm technical support and expert gunsmith advice. Whether you're in need of guidance for firearm customization tips, selecting the perfect gun parts for your projects, or seeking advanced firearm troubleshooting, our professionals are here to assist every step of the way. With a foundation of experience as seasoned gunsmiths, each member brings a wealth of knowledge accumulated over many years in the industry.
Proud graduates from top gunsmithing schools, our Gun Techs™ are not only skilled in professional gun repair but also in providing comprehensive gun care solutions and guidance. This level of expertise ensures they are well-equipped to share insights and best practices, drawing from a deep understanding of firearms and their mechanics.
When you're faced with difficult questions or uncertainties in your firearm projects, reach out to our Gun Techs™ for project guidance. Their experience in firearm maintenance help, custom gun building, and expert-guided firearm upgrades makes them an invaluable resource. Whether you're a seasoned enthusiast or new to the world of firearms, our Gun Techs™ provide the support, advice, and guidance you need to make informed decisions and achieve your objectives with confidence.
Let our industry-leading gunsmiths be your go-to source for all things firearms. They're just a call or message away and eager to help you succeed in your gunsmithing ventures by leveraging their tactical shooting guidance and firearm customization tips. Trust in our Gun Tech™ services for your next project and experience the difference that professional expertise can make.
Gun Techs are available via phone, chat, or email - phone & chat is available:
Monday - Friday, 8AM - 5PM cst
Phone: 1-800-741-0015
Email: tech@brownells.com
Chat available on "Contact Us" page, the header banner and bottom right-hand corner.
Connecting is easy.
Meet some of our Gun Techs™ Product Experts
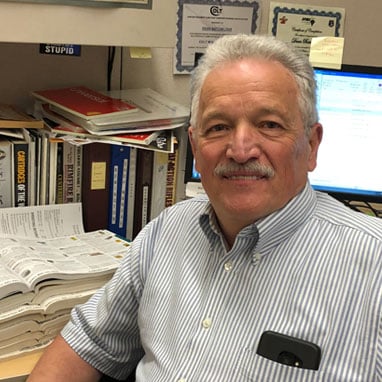
Dean BatchelderSr. Gun Tech at Brownells
I went to gunsmithing school and graduated in 1992. I had been interested in and tinkered with guns all my life and hung out with a local gunsmith when I could, but one day a good friend of mine told me, "If I were single like you, I would go to a gunsmith school and learn it firsthand." So, I did at the age of 42 and I have not regretted that decision. It has been over 30 years since I attended gunsmith school and I have been with Brownells for over 20. That is my background when I am helping customers – experience and knowledge, but I don't know it all. At Brownells, there have been quite a few tools in the catalog/line-up, that I originated the concept and helped develop, but I think the one thing that Brownells allowed me to do that meant the most to me was that they sent me to the different gunsmith schools across the U.S. where I taught the students' classes on the AR-15, and the Brownells Alternate Finishes. I was honored to be able to do that and represent Brownells to the gunsmithing schools in that capacity.
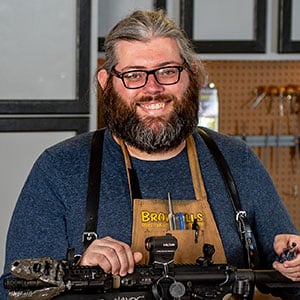
Kyle "Red" BinghamGun Tech at Brownells
The first firearm I ever shot was my dad's Remington 552 "Speedmaster" 22lr semi-automatic Rifle, I would later go on to completely refinish the firearm as a project for my gunsmithing degree from Montgomery community college and go on to learn from my time working at Remington Arm's that it was built in 1971. From there I started gunsmithing in 2010. At Brownells I have recently been promoted to Level 3 tech which is a noteworthy accomplishment in the industry. I have also Really enjoyed my work with the marketing and video teams. As a Gun Tech the most common question I receive is "I'm looking to do my first build; can you help me and walk me through my choices?" and I answer: Yes! I would love to!" because I genuinely still get excited about helping people arm themselves and build neat guns.
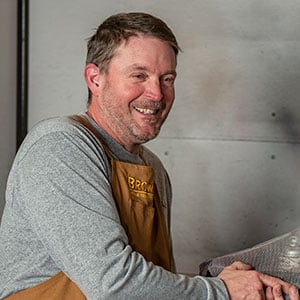
Kasey FischGun Tech at Brownells
I was drawn to the Gunsmithing industry because growing up on a farm I was in our farm shop almost every day fixing machinery and working with a multitude of different tools, so it was just kind of an outgrowth of that. I was originally hired to handle only reloading inquiries, but as I gained knowledge of more and more of our products I was asked by my supervisor if I wanted to branch out and handle the Gun Tech role. I was grateful that he had the confidence in my abilities to give me the opportunity. Being good at working with my hands and problem solving is essential. I also enjoy many types of shooting and hunting as well as customizing my firearms. I also reload ammunition for every firearm in my gun safe, so I have a wide variety of interests that help to answer customer questions.
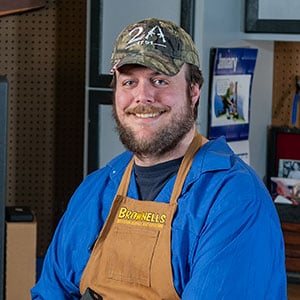
Bart HansenGun Tech at Brownells
About a year and a half ago, I signed up for Gunsmithing classes through The Sonoran Desert Institute, and graduated Magna Cum Laude. I figured it was time to combine something I was familiar with since childhood and a profitable skillset. The combination of the two led me here to Brownell's. The first firearm I ever shot was the Marlin Model 60. It was a great time familiarizing myself with firearms at a young age. I really have not been on the Gun Tech Team long enough to say I have achieved anything, but I am extremely proud to be among these people, and I am learning from them every day.
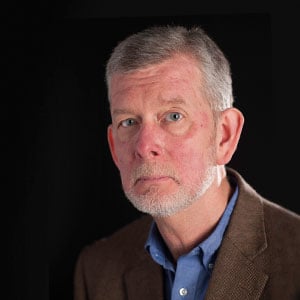
Steve OstremSr. Gun Tech at Brownells
My journey began with service in the US Army Military Police, stationed in West Germany. Following my military tenure, I pursued higher education at the University of Wisconsin, earning degrees in French and German. An enriching year at the University of Trier further expanded my cultural and linguistic knowledge. After transitioning to civilian life, I embarked on a career as a gunsmith in Tulsa, Oklahoma, and eventually became a Class A machinist, contributing my skills in both Oklahoma and Kansas. My path led me to Brownells in 2004, where I initially joined as a Guntech. In 2019, I made the shift to focus entirely on video content creation. Although the first firearm I acquired was a Browning High Power, I have developed a fondness for revolvers over time.
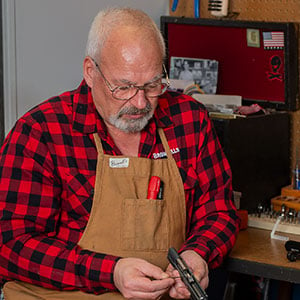
Ken PiccoliGun Tech at Brownells
The first firearm I ever shot was when I was about 7 or 8 with a Remington 513-T match master. I first started gunsmithing in the mid 1980's because I didn't like how long it would take to have some work done. Then I got my education 2007 ~2009 and opened my gunsmithing business in 2009. Having been a gunsmith for 14 years and having firsthand experience in the shooting sports since the late 1960's (when I first started shooting with my father), gives me a lot of experience to pull from. And a customer always like it when you say I have done that. During my time at Brownells, a contribution I am most proud of is having the opportunity to teach at Pine Technical where I taught how to build 1911's.
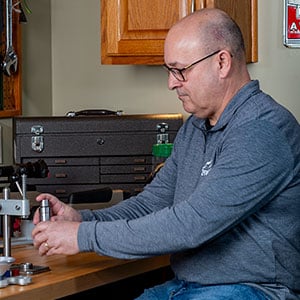
Jake SandersGun Tech at Brownells
I grew up in the industry my father operated a Barbershop and sport shop that sold everything for hunting and fishing in the 70's. During those times I observed and saw a lot of his clientele coming in with problems with their guns. My personal interest in firearms Helps tremendously with assisting customer needs and understanding their issue either with a certain part or reloading issue. I learn everyday which is why I like my job at Brownells and with that it helps to contribute to help our customers. A memorable experience at Brownells is when I participated in the 3 Gun event that Brownells hosted a while back believe in 2014. I helped with set up and takedown. It was a fun event and great experience.
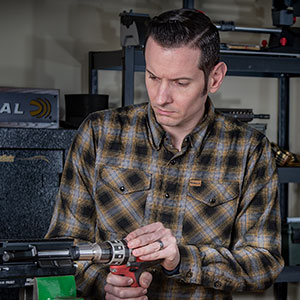
Caleb SavantSenior Video & Studio Supervisor / Gunsmith at Brownells
Before becoming a part of the Brownells team, my career started in South Louisiana, where I specialized as a gunsmith. There, I managed warranty tasks for major companies alongside helping out locals with everything from building custom guns to simple repairs. Prior to my career in the gun world, I served time in the Army, where I worked as a Combat Engineer. It's been awesome turning my love for teaching, guns, fixing them up, and tactical shooting into a job. Every day, I have the privilege of connecting with amazing people, sharing knowledge, and learning from each other.
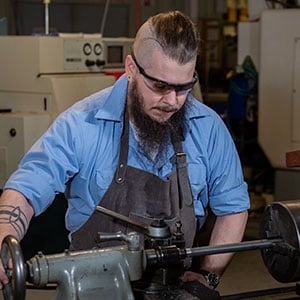
Matt SistiGun Tech at Brownells
I first started gunsmithing, like most of us did, I think. I turned a passion and hobby into a career. I built my first AR when I was 15yo in my parents’ basement. I did armorers work on my own and families’ firearms for a while but when I found out there was a degree and career path as a gunsmith, I dove in headfirst. I love the designing, building and/or fabricating parts that either don’t exist or don’t exist anymore. Since then, I’ve gotten proficient in many subjects in many subjects that are easily linked with shooting and others that seem like a stretch. This gives me a broad knowledgebase to pull from and allows me to think outside the box for solutions. When it comes to helping customers, I try to make them think deeper on what they need so we can focus on those needs and get them a better level of satisfaction with the final product.
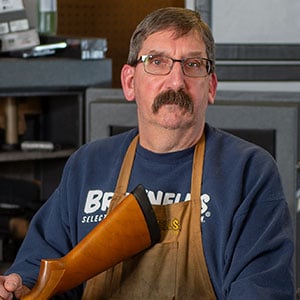
James TietjensGun Tech at Brownells
I first started gunsmithing in 1992 attending the Colorado School of Trades Gunsmithing School, after serving 4.5 years in the Army. I always enjoyed shooting and hunting and liked seeing how guns really worked. When assisting customers, it's great to be able to relate with someone who enjoys what I like to do. It makes it much easier to help them with their issue. Working at Brownells I have enjoyed many things including the Gunsmith career fair that Brownells used to do. You got to meet a lot of vendors and the different gunsmithing schools that attended the fair, it was very rewarding.